Quality control
1. Importance of Quality
Product quality is crucial for customer satisfaction and brand reputation. It affects consumer trust and loyalty, and helps a brand stand out in a competitive market.
Poor quality leads to high costs, such as product returns, customer dissatisfaction, and damage to the brand’s reputation. It also impacts a company’s profit and market position.
2. Inspection Process
- Pre – Production Check: Before mass production, we review materials, components, and patterns to make sure they match the product specifications.
- During Production Inspection: Our quality control teams monitor the manufacturing process, conduct spot checks, and solve problems in real – time to avoid defects.
- Final Random Inspection (FRI): We use the AQL 2.5 standard for apparel. We check a randomly selected sample of the final product to ensure it meets our and your quality standards.
- Packaging and Labeling Review: We check the packaging and labeling to make sure they meet legal requirements and are ready for shipping.
- Loading Supervision (Optional): If you ask, we can oversee the loading of goods to ensure the correct quantity is shipped and the products are handled properly during transit.
3. Quality Guarantees
- If you choose our Pro Plan and do ODM production with our Jinfeng factory, we guarantee the quality of your products.
- If we find defective products in our warehouse during inspection, we will replace them for free.
- If you find product defects within 15 days after receiving the goods and show evidence, we will send a replacement or compensate you.
4. How Quality Assurance Services Work
- Contact Us: You can reach us through our website, email, or phone to arrange an initial consultation.
- Custom Plan Development: During the consultation, we’ll look at your specific needs and create a custom quality assurance plan for you.
- Agreement and Setup: Once you’re happy with the plan, we’ll finalize the details and get everything ready to start.
- Quality Assurance Implementation: Our team will carry out the quality assurance procedures on your chosen products or processes.
- Reporting and Feedback: You’ll get detailed reports about the inspection results and suggestions for improvements to maintain the quality standards.
5. FAQs
We can start the onboarding process 1 – 2 weeks after the initial consultation, depending on your needs.
Our quality assurance services can be customized to fit your specific requirements.
There is no minimum order requirement. We serve businesses of all sizes.
We follow strict agreements and protocols to keep your product and process information confidential.
If we find quality problems during inspection, we’ll tell you right away and give suggestions for fixing them.
You can access a dashboard to check the real – time progress and reports of the quality assurance process.
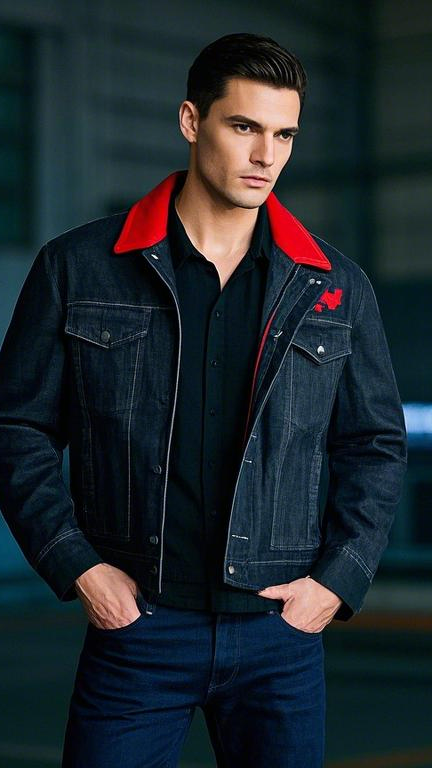